Effective Contractor Safety Management Systems: Guarding Workplace Welfare
An Overview of Contractor Safety Management
A contractor safety management system is a set of policies and procedures that a company establishes to ensure that contractors are complying with applicable safety and health regulations and requirements when they are working at the company’s facility. While most contractor management systems focus on compliance with the company’s procedural and operational requirements, the primary goal of a contractor safety management system should be protection of the safety and health of employees and contractors.
The concept and structure of a safety contractor safety management system is not very complex. Components of the system include: The goal of the contractor safety management system is to identify safety and health hazards in contracting operations and eliminate or mitigate them through the contractor selection and oversight processes . A successful contractor management system will help the company identify contractors that will help it achieve its safety and health goals and that share the company’s commitment to safety and health.
The components of the contractor safety management system should be evaluated frequently and revised as necessary to keep pace with changes in the operation of the company’s business. Examples of changes that require evaluation of the contracting safety and health system include: Changes in management practices that may increase risk; Revisions to OSHA regulations applicable to the company’s facilities and operations; and Amendments to state workers’ compensation laws that could affect company operations.
A contractor safety management system is an effective way to protect employee and contractor safety and health while controlling contractor costs.
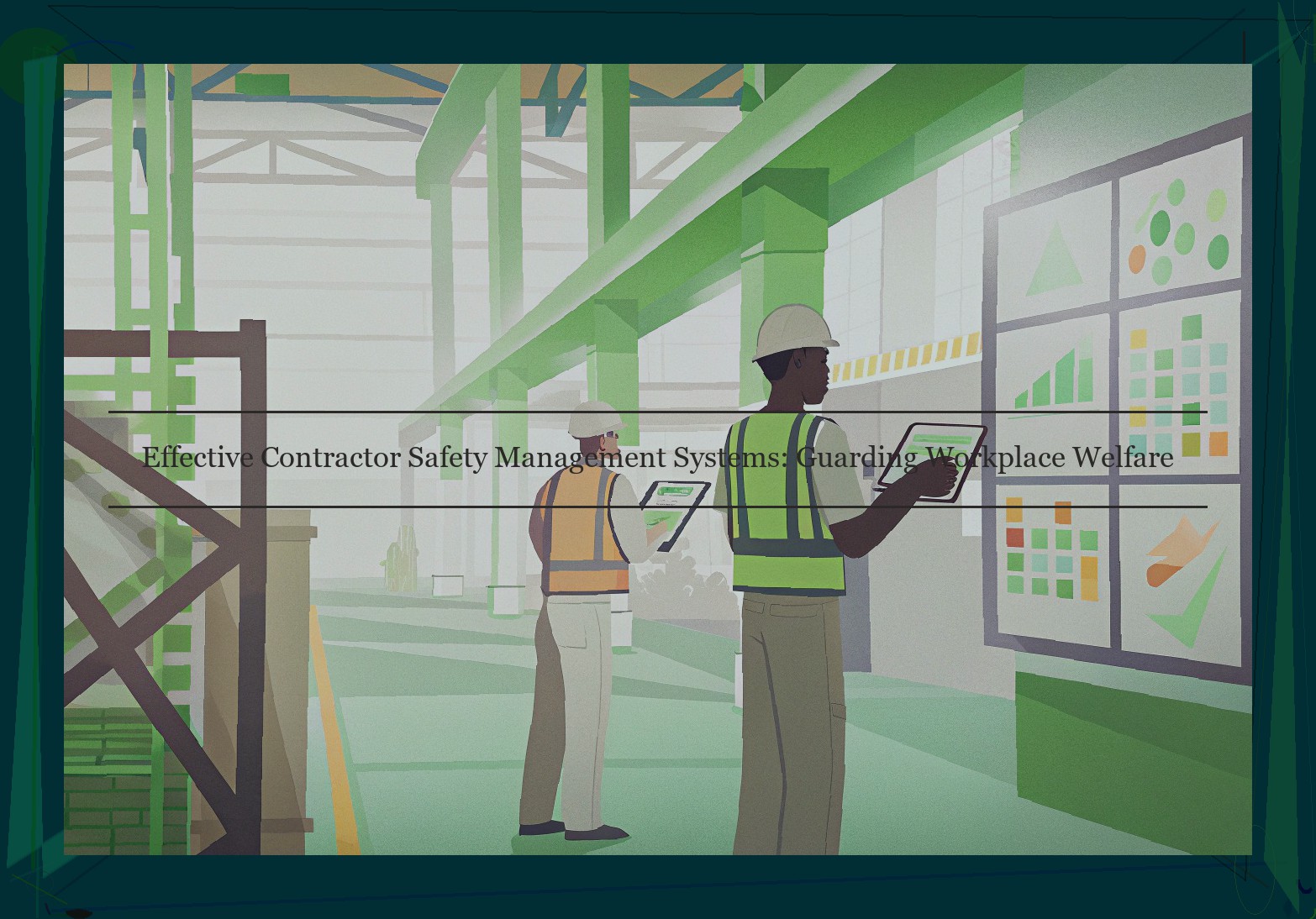
Critical Elements for a Safety Management System
The essential components of a well-crafted contractor safety management system include the following:
Risk assessment
Training
Compliance monitoring
Emergency response planning
Risk assessment is imperative for identifying and prioritizing the hazards that exist within the scope of contracted work. The scope of contracted work should be broken down into discrete tasks and then each task should be: (1) assigned a risk ranking based on a ranking process that considers potential severity and likelihood; (2) ranked by risk priority; (3) scheduled to be managed through an oversight process that considers which groups or individuals are best tasked with that responsibility; and (4) budgeted and monitored to ensure adequate resources are dedicated to the successful mitigation of the hazards realized through the risk assessment process.
Essential training elements should be developed, customized, and prioritized for contractors based on the result of the risk assessment process, applicable policies and regulations, and lessons learned in the workplace. For example, low priority, high probability hazards may be included as part of new hire orientation when no supervisory contact will be present, and a reminder posted in the department for all employees involves a broad group of employees who could benefit from the refreshment course on the hazard. On the other hand, the more serious, low frequency hazards could be incorporated into refresher training because the narrow slate of employees is considered manageable, and is further enhanced via the quality interactive, hands-on elements of the training.
A contractor safety management program that lacks monitoring and accountability is ineffective. Monitoring mechanisms are necessary to ensure the effectively designed safety program elements are implemented, and to provide the factual basis for the decisions made when elements fail to deliver expected positive outcomes. All elements of an organization’s safety related activities and operations should be connected in a meaningful way to the goals, objectives, and evaluation criteria which, themselves, should align with the overall goals and objectives of the business entity. The information provided through program monitoring should lead to action items that, when addressed, can augment the effectiveness of the contractor safety management program and the role it plays in meeting the organization’s expectations.
Responding to emergencies is fundamentally different than what we see in more routine workplace exposures and risks. Unplanned and unexpected, two of the most significant challenges are: (1) the need for a prompt and decisive response; and (2) the demand for crisis management skills and knowledge that are foreign to those who have not been trained to respond to such situations. When emergencies occur, it is the training and preparation that the entity engaged in the unforeseen circumstances rehearsed prior to the emergency that will enable a swift response, limit losses, and facilitate an efficient recovery.
Advantages of Employing Safety Management Systems
An effective contractor safety management system establishes robust vetting measures that can lead to more consistent performance and reduced liability. When an organization takes the time to conduct thorough administration and planning, they can anticipate better safety outcomes. Likewise, when a business partners with organizations that prioritize safety, their own role in the project is followed by code and regulations. Therefore an organization maximizes their opportunity for fewer incidents while proving their own commitment to workplace well-being.
Many companies are also finding that it is less expensive to hire qualified contractors that practice risk control and prioritize safety over others. As such, many organizations are looking for ways to incorporate safety benchmarking and more rigorous safety systems into prequalification measures. They can filter out high-risk contractors that would end up costing them after administrative costs and worker’s compensation. Additionally, as workers’ compensation costs continue to rise, companies find value in hiring contractors that value safety so that they don’t directly contribute to that cost.
Any time you can weed out less suitable contractors from your shortlist you reduce the likelihood of unqualified onsite personnel that increase the risk of an incident. In turn, you can spend more time focusing on the significant risks to your project and less on everyday annoyances. Moreover, because of the nature of prequalification, you are establishing a partnership with contractors that value the relationship. When you improve the contractor vetting process you can also improve your relationship with contractors. This can have a snowball effect as you continue to choose the same contractors and they reciprocate with lower contract prices as a result.
Obstacles and Solutions to Safety Management
The implementation of effective contractor safety management systems (CMS) is also not without its challenges. Change management, resource allocation and maintaining consistency are all issues that can thwart even the best efforts. The old adage "what gets measured gets improved" has a bearing here and is relevant to all aspects of safety compliance. When introducing any change its critical that there is strong engagement from everyone in the organisation as well as contractor senior management. "Buy-in" is a large part of successfully maintaining momentum in the face of resistance. This has to be genuine however and requires regular feedback and recognition. The popularity of initiatives such as the "employee of the month" stand as testament to this but such awards need to be awarded to those with demonstrated over and above compliance behaviour and adherence to and championing of safety messages. The adage "you can’t manage what you don’t measure" is also part of the reason why CMS are proving to be so effective. The ability to apply economic leverages like pay-for-performance rates based on performance and adherence to KPI’s has been a major factor in driving compliance in many sectors where they are introduced. Unintended consequences may be a by-product where these rates are applied as a blunt instrument in their application but the idea is that idiots get eliminated from the supplier regime and the best performers receive more targets to aim at. It’s a system that will deliver results, but not without some cost and risk being transferred down the line. If care and caution is not applied in the responsible application and usage of these rates, it can be a double-edged sword. Equally important is the allocation of resources. We’ve seen poor quality systems fail to deliver expected outcomes purely because they are poorly resourced. The allocation of adequate funds can be linked to the economic incentives mentioned above – where good performers have also demonstrated high levels of quality in other areas of the services performed. All of these issues can only be addressed through diligent and mature risk management. The integration of risk considerations into all decision-making processes, particularly those concerning contractor selection, can help avoid risks manifesting themselves down the track.
Technology Utilization in Safety Management
Technological tools can play an important role in any contractor safety management system, better enabling organizations to keep their contractor workforce safe. Technology can help organizations ensure compliance, real-time monitoring and more effective reporting.
Many organizations have created safety and health systems that promote safety compliance through the ability to track and monitor activities and reporting the data to the appropriate individuals responsible for making decisions or taking appropriate action. Necessary functions can be performed by a technology-based system or software tool. This is called a "compliance management system." For example, tracking safety-related activities could be accomplished using a computer spreadsheet with an extensive list of individuals/sites/activities/equipment, etc. that requires individuals to indicate compliance or non-violation. A more elaborate system would require users to enter information into a database that would require additional time and effort, but would provide more immediate reporting to management or others overall compliance, trends, deficiencies , etc.
Technology applied in a compliance management system can also immediately notify the proper individuals of the need for an immediate corrective or preventative action when non-compliance has been identified. For example, if an employee is reported up the chain as being in a safety violation, this information can be automatically routed to the immediate supervisor, divisional head, human resource manager, etc. based on the severity of the circumstances and/or the frequency of violations. Another example is to notify the site manager of the need to take preventative action if a piece of equipment has become non-compliant with the latest safety requirements.
Some software tools are being developed as job hazard analysis tools. These tools allow organizations to customize forms for job-related hazards and requirements, and then easily enter the information from the field into the electronic programs from devices such as palm pilots or tablet computers.
There is a range of technology-based compliance management systems available. With most, however, the higher the level of customizability the more expensive the system. While software tools are helpful, they cannot replace the need for management commitment that must come from the top, and the dedication and participation of the employees performing the work.
Success Stories of Safety Management Systems
A number of organizations have successfully implemented systems that have significantly reduced both the risks and severity of contractor injuries.
The Royal Dutch Shell Group has an internal policy of developing its contractors’ skill and safety-related expertise. The company engages in online data exchange with contractors to support and enable mutual sharing of critical information. In addition, it conducts a joint safety health risk survey with contractors every five years. The results are used to set contract-specific goals. In several contracts, there has been a 75% to 100% reduction in accident rates following the commencement of implementation of these measures.
One of the objectives of the United States Department of Defense is zero harm and no unnecessary impact on the environment. In its effort to achieve that objective, the department introduced a contractor safety management system. The department has adopted the ISO 14001:2004 Environmental Management System as a framework for contractor training. While it was relatively large, the program reduced serious accidents by over 50% and has been adopted widely. The work has now been incorporated into the ISO 28000 Supply chain security management system as a "best practice" for overall security management.
Delegated legislation has also been employed to enforce safety management systems. In Australia, the Work Health and Safety Act 2011 (Cth) was introduced to give effect to various recommendations made by the Productivity Commission. The new laws also apply to contractors and require them to ensure only workers who have been trained and assessed for conduct in high-risk work are permitted to carry out high-risk work. The applicable regulations prescribe detailed requirements for training and assessment processes. A work health and safety management system is also now required under the new law. All workers are required to be trained to enable participation in procedures for the identification of hazards, assessment of risks and the implementation of risk controls for those hazards. Senior employees are required by the law to be given adequate training to enable them to effectively contribute to the safety training of their colleagues.
In each of these cases, there has been a demonstrable improvement in safety performance as a result of the introduction of a safety management system.
Regulatory and Legal Implications
Legal and regulatory considerations for contractors working on a large oil and gas project typically drive the contractor with the largest workforce to develop the safety management system for the project. However, it is important to remember that the legal analysis is relevant to all parties involved in large projects—even general contractors without responsibility for the overall safety program. The statistics for overall injury and illness remain high in the construction industry compared to other industries, so all parties need to understand their safety obligations, even if most of the liability and exposure is allocated to large project contractors.
The scope of the OSHA regulations rarely is an issue that arises during the bidding phase. In spite of the fact that negotiating the applicability of requirements of OSHA standards to specific jobs is a lengthy and complicated process, that is precisely what is required of any contractor or owner serious about managing safety and preventing injuries. Under OSHA regulations, an owner or contractor is responsible for complying with all applicable OSHA standards and for creating a safe workplace. So, evaluating what construction standards apply to the work on a particular site requires a detailed review of the work to be performed, the industry covered by the standard, and potential citations addressed in the standard. In addition, how the requirements of the standard connect to the safety management documents and programs the contractor intends to implement must be coordinated. For a general contractor that coordinates multiple subcontractors, it is not unusual for there to be conflicting standards between contractors that need to be reconciled.
For all contractors, when it comes to safety obligations, a thorough understanding of the OSHA recordkeeping requirements is necessary to evaluate subcontractor safety performance. If a contractor does not have accurate data on their subcontractors’ injury rates and near-misses, the contractor cannot adequately assess the subcontractor’s safety performance. The contractor must have this information to make an informed decision about whether the subcontractor has the capacity to perform on the project. This is especially important for "journeyman" subcontractor relationships that will last for the life of a project for a highly skilled workforce.
OSHA’s Reporting Standards also require diligence in evaluating subcontractor safety performance. OSHA requires employers to contact it if a subcontractor has a work-related fatality or accident with three or more hospitalizations within 30 days of an incident. Internally, a contractor should have a clear set of guidelines for reporting and responding to these incidents, even if they occur at subcontractors’ facilities, to ensure contractors and subcontractors are fully compliant throughout the project.
On September 30, DOT-PHMSA issued the Pipeline Safety: Safety of Gas and Hazardous Liquid Pipelines – Underground Storage Facilities; Correction; Extension of Applicability Comment Period and Announcement of Public Workshop, 78 Fed. Reg. 60673 (Oct. 1, 2013). PHMSA decided to delay collection of information under the Safety of Gas and Hazardous Liquid Pipelines notice, 78 Fed. Reg. 58516 (Sept. 24, 2013), citing concerns by the Office of Information and Regulatory Affairs and stakeholders regarding certain questions that the agency intends to re-examine. The agency provided another 90-day extension of the comment period and extended the comment period for a sister ANPRM, Hazardous Liquid Pipelines: Requirements for Gas Integrity Management Programs, by 90 days. PHMSA is holding workshops to discuss both rulemakings.
On October 22, PHMSA published a notice of proposed rulemaking, Underground Natural Gas Storage Facilities Safety (Gas Storage NPRM). PHMSA is proposing to amend existing safety regulations for pipeline facilities to minimize the risks associated with underground natural gas storage facilities and to keep women, children, and others that live near underground natural gas storage facilities from being impacted by large quantities of natural gas leaking from underground storage fields. Anyone who owns or operates an underground natural gas storage facility is subject to the proposed rule. Specifically, the proposed rule covers 24 states that are home to one or more underground natural gas storage facilities. PHMSA is also clarifying the language used in the current regulations and is making formatting revisions to enhance the readability of the regulations. In addition to revising current regulations, if the NPRM is finalized before April 14, 2015, the list of reporting requirements in § 192.16 would be added to the annual reports that are required to be filed by operators conducting a pipeline integrity assessment in a State that has opted-out of the Federal Government’s record keeping requirements.
Future Perspectives on Safety Management Evolutions
Beyond regulatory compliance, there has been a notable shift in the focus of contractor safety management systems. Corporate contractor safety programs are increasingly adopting a new mantra: We Care 2.0, meaning that the health and safety of contractors and suppliers is as important as the health and safety of corporate employees. A key to this new mantra is the need for companies to take a more active role in their engagement with contractors. Much like any other business relationship, there is a difference between the essentials and the basics. Active engagement with contractors, primarily undertaken prior to project initiation and management, will position companies to build effective safety cultures with the contractors and suppliers they retain. This directly impacts an organization’s competitive position.
Another trend, moving from a reactive approach to a proactive one, is to gradually remove "holes" in the Contractor Safety Management System (CSMS) process. These "holes" have a high probability of resulting in unintended operational failures. A proactive approach eliminates costly and often frustrating downtime through increased visibility and, ultimately, increased value and safety . The result is a calmer environment, easier resources, less paperwork, no backtracking by the HSE team, and employees and contractors who are able to focus on their work. A proactive approach consists of good pre-qualification processes, proper contractor selection, drafting appropriate contractual requirements, and conducting appropriate pre-mobilization activities.
The objective is to reduce organizational disruption while enhancing safety management system effectiveness. The incremental and thoughtful removal of CSMS "holes" improves the overall state of corporate contractor safety. A forward-looking approach ensures businesses remain organized and can focus on the day-to-day business of getting the job done without sacrificing employee and contractor safety. A forward-looking contractor safety program focuses on the development of best practice approaches to common contractor safety management issues, including: Emerging best practices applied to these items will be the focus of safety professionals and management over the next several years. There is no doubt that some of the best practices, tools, and enhancement items that emerge will be based on the wealth of data being generated by and in support of Contractors Safety Management Systems.